Sheet metal fabrication typically involves several welding techniques, each suited for different applications and materials. Some common welding techniques used in sheet metal fabrication include:
- TIG Welding (Tungsten Inert Gas): TIG welding is a precise welding process that uses a non-consumable tungsten electrode to produce the weld. It is suitable for thin materials and provides excellent control over the heat input, making it ideal for intricate designs and precise welds.
- MIG Welding (Metal Inert Gas): MIG welding is a versatile welding process that uses a consumable wire electrode and a shielding gas to create the weld. It is well-suited for welding a variety of metals and thicknesses and is relatively easy to learn and use.
- Spot Welding: Spot welding is a fast and efficient welding process that uses electrodes to apply pressure and heat to the workpieces, creating welds at discrete points. It is commonly used in automotive and electronics industries for joining thin sheet metal components.
- Resistance Welding: Resistance welding encompasses several techniques such as seam welding, projection welding, and butt welding. These processes use electrical resistance to generate heat at the welding interface, joining the workpieces together.
- Stick Welding (SMAW – Shielded Metal Arc Welding): Stick welding is a manual welding process that uses a consumable electrode coated in flux to create the weld. It is suitable for outdoor and windy conditions and can weld various metals, although it may not be as precise as TIG or MIG welding for thin sheet metal.
- Flux-Cored Arc Welding (FCAW): Similar to MIG welding, FCAW uses a continuously fed consumable wire electrode, but it incorporates a flux within the wire to shield the weld pool from atmospheric contamination. It is commonly used in heavy fabrication applications.
These are just a few examples of welding techniques used in sheet metal fabrication. The choice of welding method depends on factors such as material type, thickness, desired weld quality, production volume, and budget constraints.
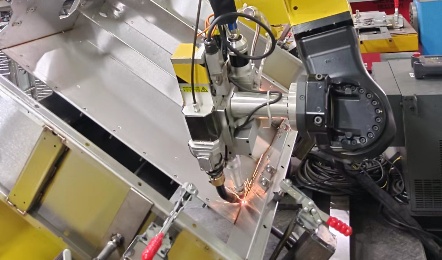